Preventing Weld Undercut Demystified: Strategies for Success
Preventing Weld Undercut Demystified: Strategies for Success
Blog Article
Recognizing the Causes and Solutions for Undercut Welding in Steel Fabrication Processes
In the world of metal fabrication procedures, the incident of undercut welding positions a considerable difficulty that demands a thorough understanding of its reasons and sensible options. The elaborate interplay of different aspects throughout welding operations can result in this unwanted sensation, impacting the structural integrity and general quality of the bonded joints - Preventing weld undercut. By studying the source of undercut welding and discovering effective restorative measures, producers can raise the criterion of their handiwork and guarantee the production of flawless steel parts
Typical Causes of Undercut Welding
Regularly forgotten in metal fabrication, undercut welding happens due to various elements that demand precise interest and proficiency to be efficiently alleviated. In addition, inappropriate welding strategies, such as using the wrong welding angle or travel rate, can likewise add to damage development. The option of welding specifications, such as voltage, existing, and cord feed rate, plays a substantial duty in the event of undercut welding.
Influence of Incorrect Welding Parameters
Inaccurate welding parameters can significantly compromise the integrity and quality of bonded joints in steel manufacture procedures. The effect of inaccurate welding specifications materializes in various ways, leading to architectural weak points and issues in the bonded elements. One important element impacted by improper welding parameters is the infiltration deepness of the weld. Inadequate heat input as a result of reduced welding currents or excessively high travel rates can cause inadequate blend in between the base metals, leading to insufficient joint infiltration and compromised bonds. Conversely, too much warm input brought on by high welding currents or slow-moving traveling speeds can bring about extreme and burn-through support, producing a fragile and unpredictable weld framework. Additionally, wrong specifications such as improper voltage setups or incorrect electrode angles can add to unpredictable weld grain profiles, absence of combination, and increased opportunities of problems like damaging. Precise focus to welding parameters is vital to ensure the production of high-grade welds with the preferred mechanical buildings and structural stability.
Effect of Improper Torch Angle
Improper torch angle in welding procedures can dramatically impact the high quality and integrity of the last weld joints in steel fabrication procedures. Damaging is an usual welding flaw where a groove creates along the weld toe, deteriorating the joint and endangering its architectural stability.
A torch angle that is also steep can cause inadequate penetration, insufficient fusion, and increased spatter. On the various other hand, a torch angle that is too shallow can lead to too much penetration, burn-through, and distortion of the base material. Preventing weld undercut. Correct torch angle is important for making certain consistent weld high quality, toughness, and look
To avoid damaging and various other issues triggered by inappropriate lantern angles, welders have to be trained to maintain the right lantern angle throughout the welding process. Normal surveillance and adjustment of torch angles during welding can help accomplish sound welds with minimal flaws.
Duty of Inadequate Welding Strategies
One more element of poor welding methods is inappropriate weld preparation. Inadequate cleaning of the base steels, inaccurate joint layout, or insufficient edge preparation can all contribute to damage welding. Poor shielding gas insurance coverage or check my source using the incorrect type of gas can result in insufficient blend and the formation of undercut defects.
To resolve the role of inadequate welding methods in steel fabrication processes, it is vital to provide detailed training for welders. Appropriate education and learning on welding parameters, joint prep work, and shielding gas selection can assist protect against undercut welding view website and guarantee premium welds in steel manufacture projects.
Reliable Solutions for Undercut Welding
Resolving undercut welding in steel manufacture requires executing effective solutions to enhance weld top quality and architectural stability. One of the main options to battle undercut is to readjust welding criteria such as voltage, present, and travel rate to make sure appropriate warmth input and fusion. By fine-tuning these settings, welders can prevent too much melting of the base steel and filler material, minimizing the chance of undercut development.
Furthermore, appropriate joint prep work is vital in preventing undercut. Making sure tidy base steel surface areas devoid of impurities and making use of the suitable bevel angle can aid advertise much better weld penetration and minimize the risk of undercut - Preventing weld undercut. Employing suitable welding strategies, such as oscillating the torch or weaving, can likewise aid in dispersing warmth equally and loading the weld joint adequately, minimizing the opportunity of undercut issues
Moreover, selecting the appropriate welding consumables, consisting of electrodes and filler metals, is important in minimizing undercut. Making use of products with appropriate chemical make-ups and mechanical buildings can contribute to attaining audio welds with minimal undercut. Routine examination and quality assurance steps must likewise be implemented to identify and address undercut concerns quickly, making certain the general honesty of produced metal elements.

Final Thought
In verdict, recognizing the causes and options go now for undercut welding in steel manufacture processes is vital for attaining premium welds. By addressing usual causes such as inaccurate welding criteria, inappropriate lantern angle, and inadequate welding techniques, welders can avoid damaging and make sure solid, resilient welds. It is important to take note of these elements and apply reliable remedies to boost the overall welding process and final item quality.
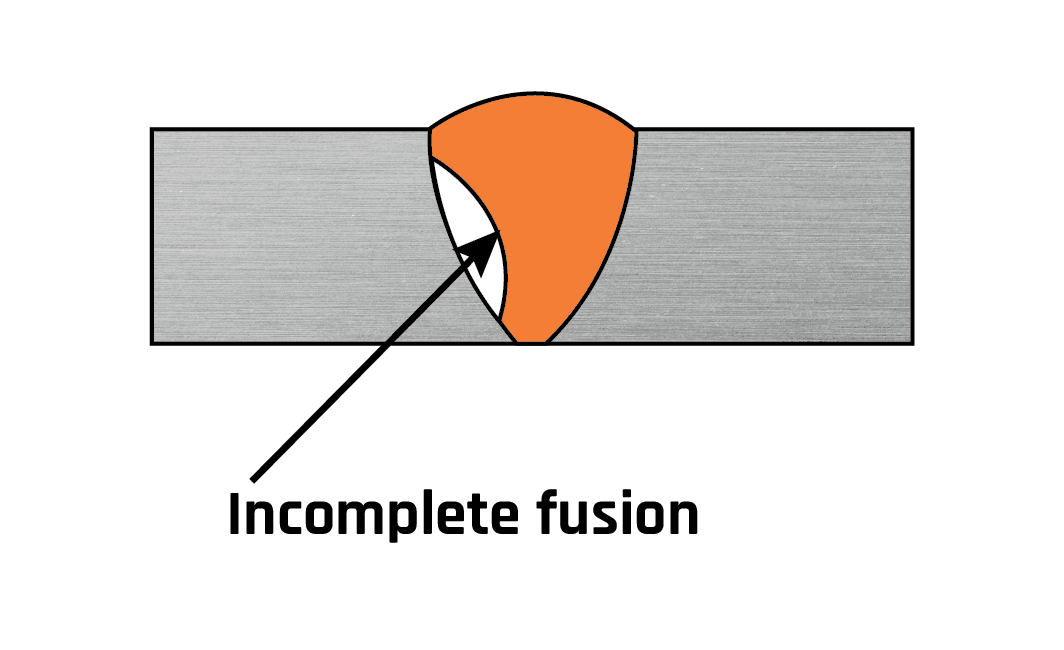
Report this page